Abstract : The treatment of volatile organic waste gas in the printing and canning industry
“The use of regenerative incinerators has become increasingly widespread. This was unpredictable many years ago,†said Mike Scholz, senior application engineer at Anguil.
As the first-generation incinerator system is nearing its useful life, many can making plants face the problem of repairing or replacing their existing air pollution control systems.
Like many other factories in this industry, a Silgan can making plant in the Midwestern United States has been using a direct-fired incinerator
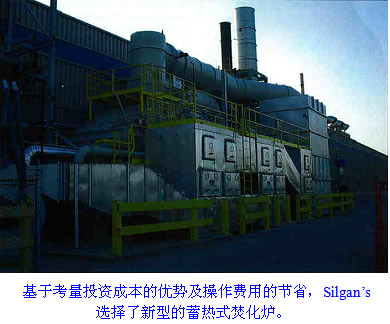
(thermalrecuperativeoxidizer) Direct heat recovery to control the exhaust gas emitted from its sheet coating line. After more than a decade of use, the incinerator had to be repaired, so Silgan began looking for effective, highly functional solutions.
According to past experience, direct-fired incinerators with direct heat recovery have been the first choice for canmaking plants, especially in factories where the operating temperature in the fire zone exceeds 350 degrees Fahrenheit (177 degrees Celsius).
In the past, direct-fired incinerators were superior to regenerative incinerators (RTOs) in terms of investment costs, and they were said to have more flexibility in carrying restrictions on volatile organic compounds (VOCs). However, there has been a shortcoming in the use of auxiliary fuels. The internal heat recovery rate of the direct-fired incinerator is up to 70%, while the regenerative incinerator can reach above 95%.
For can makers, this shortcoming can be offset by the addition of heat recovery devices. The hot, purified air released by the incinerator is directed back to the burner zone without leaking into the atmosphere. This reduces the operating costs of the direct-fired incinerator, and in the past, this system was almost uniformly specified because the lower explosive limit of the VOCs (LEL-Lower Explosive Limit) was more than 10%.
Based on the above notions, when he heard that Anguil recommended the use of regenerative incinerators (RTOs) in the coating factories in the west, Silgan's reaction was quite sceptical: "What do they recommend? This RTO is obviously not applicable." Of course, according to the technical information obtained when Silgan first used a direct-fired incinerator, such reactions are understandable. But this also provides an ideal framework to study what changes have been made to the design of incinerators over the past decade, which is enough to reverse such fierce initial reactions:
â— The direct-fired incinerator no longer has the advantage of investment cost;
â— With hot gas bypass pipe and forward supply technology, the current lower explosion limit of RTO has been set at more than 25%;
â— Because the fuel cost has been unstable and continues to rise, every percentage of heat recovery is of great significance;
â— The new demand for VOC capture and removal has led to the gradual marginalization of direct heat recovery, and the operating costs of both direct-fired and regenerative incinerators have become increasingly larger.
Silgan's existing direct-fired incinerators were originally designed based on air volume, organic exhaust gas concentration, and expected removal efficiency. During operation, the VOCs exhaust gas enters the system fan and is then discharged into the heat exchanger. Exhaust gas is warmed up before passing through the surface of the heat exchanger, and then enters the burner, where the contaminated air is warmed to the hot combustion temperature (1,200 to 1,800 degrees Celsius/650 to 1,000 degrees Celsius). An exothermic reaction occurs when exhaust gas containing VOCs is warmed to the hot combustion temperature for a specific time (0.5 to 2.0 seconds). VOCs in the air are converted to carbon dioxide and water vapor. The hot, purified air then passes through the shell side of the heat exchanger where the heat energy released is used to preheat the incoming solvent-containing air to reduce system fuel consumption. Finally, the pollution-free air is discharged into the atmosphere.
All of the direct-fired incinerators have a weakness in their design, that is, the steel in the heat exchanger is exposed to high temperatures in the combustion chamber (usually over 1,600 degrees Fahrenheit/871 degrees Celsius). This block of equipment in the Silgan plant has required constant maintenance over the years, resulting in increased costs and productivity impacts. Silgan's engineers must repair the old system, replace a similar device, or look for alternative solutions.
After evaluating several options, the RTO was selected because of its investment cost advantage and savings in operating costs. This is a customized management system, especially designed for their high air volume and high concentration. Anguil designs, manufactures and installs this 40,000SCFM regenerative incinerator (RTO) and heat exchangers, hot gas bypass pipes and furnace cleaning equipment.
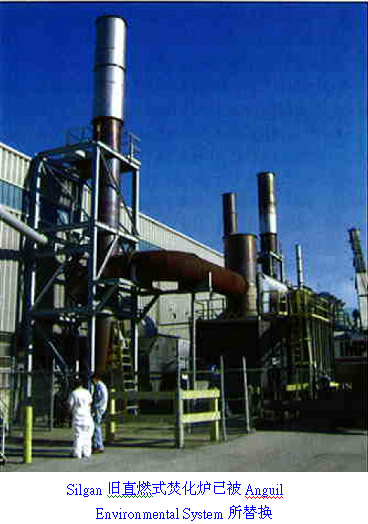
The new RTO of Silgan operates as follows: The solvent-containing process waste gas enters the incinerator via an inlet pipe and is flow-controlled. The Poppetvalves direct the gas to one of the heat recovery tanks, where the process exhaust gas is preheated. Process exhaust gas and contaminants slowly warm up in the inlet ceramic bed before flowing to the combustion chamber. The VOCs burn in the combustion chamber and then release heat energy in the ceramic bed where the outlet of the combustion chamber flows. The exiting ceramic bed is heated and the exhaust gas is cold, so the outlet gas temperature is only slightly higher than the process exhaust gas inlet temperature. Through the flow control and Poppet Valves, the airflow is regularly switched into the direction of the ceramic bed in order to increase the incinerator's heat recovery to the maximum limit. The incinerator's VOC combustion and high heat recovery reduces the need for auxiliary fuel and saves operating costs. For example, at a 95% heat recovery condition, the temperature at the RTO outlet may only be about 70 degrees Fahrenheit (40 degrees Celsius) above the inlet process exhaust gas. The incinerator can operate on its own energy supply and does not require any auxiliary fuel at normal operating concentrations.
The temperature of the process exhaust gas and the fire zone discharged by the ilgan plant poses some challenges, but it also implies some opportunities.
As the lower explosion limit of the process is as high as 14%, the high temperature of the RTO has attracted attention. A hot bypass valve allows excess heat from the RTO reactor to be vented directly to the exhaust pipe, or returns to the burner's inlet pipe when the amount of incoming VOCs provides more heat than required to maintain the set temperature. Because the incinerator does not require much fuel to reach the desired temperature, this original heat recovery saves thousands of dollars in operating costs. According to Anguil's design, there will not be any loss in temperature retention time, which will ensure removal rates and eliminate equipment overheating concerns. Whether the bypass is open or not, the VOCs removal efficiency can be guaranteed.
Silgan also studied other energy-saving strategies and used a secondary heat exchanger to recover the extra heat from the RTO exhaust stack. Preliminary estimates show that the use of a heat exchanger in the incinerator's exhaust pipe can recover an additional 6.5million btu/hr of hot gas. Fresh air (average outdoor temperature of 46 degrees Fahrenheit or 8 degrees Celsius) passes through a single heat exchanger with 50% efficiency, and the air is heated to approximately 350 degrees Fahrenheit (177 degrees Celsius). This recovered heat energy can be used for heating in production or in winter, thus achieving significant savings.
The RTO also includes a high-temperature bake-out system that approximates the self-cleaning function of the furnace. This feature removes organic buildup on the cooling surface of the heat exchange heat storage material. In the bake-out mode, the RTO and the process are offline. When the air volume decreases, the outlet temperature rises before the direction of the air flow changes. This hot air evaporates organic particulates and completely removes obstructions on the heat storage bed. The direction of air flow is switched and the relative cooling surface is also cleaned. The standard bake-out occurs at 650 degrees Fahrenheit (343 degrees Celsius). The heat storage stand and poppet valves of the Silgan system are made of stainless steel, so the bake-out temperature can reach 800 degrees Fahrenheit (427 degrees Celsius). This ensures more thorough cleaning. The set RTObake-out can reduce the pressure drop of the heat recovery tank. Therefore, when the device bake-out is recommended, Anguil will install the necessary transmitters to monitor the pressure drop of the regenerator bed, as well as providing the operator with continuous record data and related data.
DanGallo, Silgan's manufacturing area manager, is very satisfied with this result. “We chose Anguil because of their superb technology and commitment to service,†he said. “Anguil is not only capable of solving problems with its own equipment, but it can also propose operating solutions for incinerators made by other homes. We really appreciate them. The perfect pursuit, but also very happy to be a good partner in Anguil business."
Note: Silgan is the largest supplier of food metal containers in North America
PU Ceiling Medallions
Drop Down Ceiling,Install Ceiling Medallion,Moroccan Ceiling Medallion,Ceiling Medallion Installation
Goolee Decoration Material Co., Ltd. , http://www.jxpucolumn.com