1. Project Overview
Victory 902 is a non-self-propelled pipe-laying vessel. The main body is a box-type structure with a total length of 118.8m, a width of 30.4m, a depth of 8.4m, a draught of 5.0m and a total tonnage of 14 500t (see Figure 1). A pipe laying line is provided on the starboard side of the main deck, equipped with welding equipment, NDT equipment, coating equipment and other ancillary equipment; a pipeline storage area capable of storing approximately 2000 tons of pipelines is provided on the port side of the main deck. The loading and unloading and movement of the pipe is done by a 35t full-rotation crane, roller and conveyor. The main deck of the ship has a 6-story living building. It can maintain 60 days of self-sustaining capacity when it is full of 200 people. The top has a helicopter landing pad. The ship's raft is equipped with a large crane with a lifting capacity of 400t (fixed) / 350t (full rotation). The maximum water depth of the pipe laying operation is 100m.
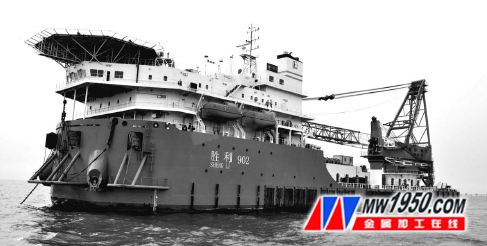
Figure 1 Victory 902 pipe laying project completed
2. Welding difficulties
During the construction of the Victory 902 pipelaying engineering ship, the following welding difficulties existed: 1 The crane column (see Figure 2) penetrated from the bottom to the top. All bulkheads, decks and floors have dense reinforcing structures, and many spaces are small and the structure is small. Complex, difficult to construct, and high dimensional accuracy requirements. 2 Winning 902 pipe-laying engineering ship's crotch, stern, and both sides are linear structures, especially the two sides of the raft are hyperbolic structures, which require high control of welding deformation. 3 The main deck of the starboard pipe laying line is designed as a concave deck with irregular slopes, high strength and complex structure. 4 The A-frame structure of the starboard pipe-laying line is mainly made of high-strength marine steel plate. The steel plate is thicker and the difference in plate thickness is large. The difference in plate thickness is 80mm, and the reinforcement structure is more connected with the A-frame. The construction space is difficult and the construction is difficult. 5 The cradle hinge seat (see Figure 3) is an important structure for connecting the stinger and the hull. It has high load strength and high dimensional accuracy. It uses a large number of thick plates up to 150mm, which is the thickness of the conventional hull structure. 10 times. This greatly increases the amount of weld shrinkage, which will seriously affect the installation accuracy of the hinge seat and the stress on the stinger.
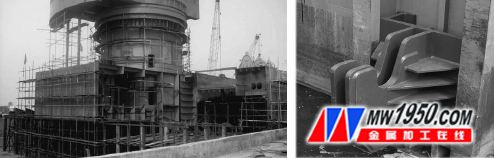
Figure 2 Crane column under construction Figure 3 Trust frame hinge seat
3. Key welding process
(1) Introducing TribonM3 ship three-dimensional production design software with new construction software, using segmentation as the unit, using pallet management system to improve the integration effect of “shell, raft and coatingâ€; for escrow frame, A-frame With the truss structure, the three-dimensional software is used for stakeout, the data is input into the CNC cutting machine, and the groove of the intersecting line is automatically cut to improve the cutting precision, ensuring uniformity of the pair, and effectively controlling the welding quality and welding deformation; The structure with high precision requirements, combined with the knowledge of thermodynamics and dynamics theory, uses ANSYS software to analyze the welding stress, estimate the welding shrinkage and direction of each weld, and increase the welding shrinkage residual material during the blanking process according to the construction sequence. To reduce welding deformation and welding stress.
(2) Welding technology of large-thickness steel plate large structure The thick steel plate structure is mainly concentrated on the susceptor frame, A-frame and box beam structure. The most effective way to improve the welding quality of thick steel plate is to increase the prefabrication strength and carry out the pre-fabrication of the prefabricated components. Heat treatment, which is convenient for welding operation and structural mechanical properties.
(3) Hull welding anti-deformation control During the segmental prefabrication and closing process, the key to the control of welding quality is to control the welding deformation of the hull through a reasonable welding sequence. The deformation of the weld is shown in Figure 4.
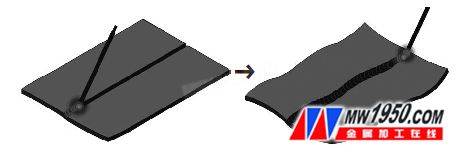
Figure 4 shows the deformation of the weld
The main measures taken to prevent welding deformation are: 1 puzzle. According to the order of “welding the first seam and then welding the longitudinal seamâ€, the welding deformation can be effectively controlled. 2 profiles are prefabricated. Symmetrical simultaneous welding with two welders. 3 sections assembled. According to the procedure of “welding the weld first, then welding the flat weldâ€, “first welding the bulkhead structure, re-welding the main structure, and welding the small structureâ€. 4 double bottom structure. Arrange 4 welders to synchronize symmetric welding in the same direction. 5 hull closing group pair. First, use the laser theodolite to check the horizontality of the tire frame, and then press the pair of "from 艉 to è‰, from bottom to top, first and then the middle and back sides". 6-section closed welding. Symmetrical welding is carried out in the order of "welding part, post-welding sheet", "first welding longitudinally closed seam, and post-welding transversely closed seam". The welding equipment is shown in Figure 5.
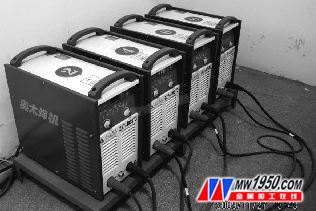
Figure 5 Welding equipment
(4) Construction of the susceptor system The welding quality control cradle system is mainly composed of the escrow frame (two sections), the A-frame and the A-supported box girder structure, and adopts the construction scheme of “components are prefabricated and assembled on siteâ€, thus increasing each Prefabrication accuracy requirements for individual components.
The stinger frame, the A-frame and the side tie rods are individually prefabricated. The A-frame frame beam structure consists of 11 boxes. The box girder structure is the main force area for the engineering ship pipe laying operation. This area adopts high-strength thick steel plate and strengthens the structure, so that the load can be transmitted to all parts of the main body reasonably.
Prefabricated welding sequence of box girder: 1 box body panel and internal components are welded after completion; 2 a ring temporary reinforcement structure is added every 1m to control the welding deformation to the greatest extent; 3 box body web welding sequence is shown in the figure As shown in Fig. 6, after the weld bead 1 is completed, it is turned over, and the weld bead 2, 3 is welded, and after completion, the weld of the weld bead 4 is again turned over. 4 Four welders adopt the segmental back-welding method to synchronously weld welding from the center of the box to both ends, as shown in Figure 7. 5 Multi-layer multi-pass welding is adopted. After each whole welding, the next welding is carried out. It is forbidden to change the position after multiple welding is completed.
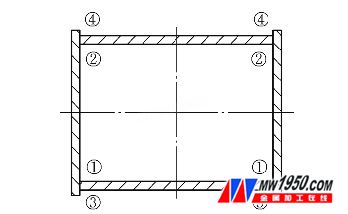
Figure 6 Box web welding sequence Note: 1 to 4 is the welding sequence
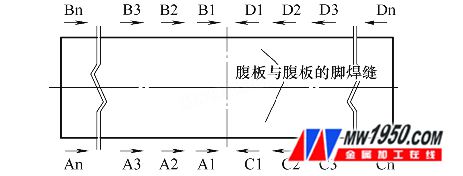
Figure 7 Symmetrical simultaneous welding of the two ends of the box Note: A, B, C, D are four welders
In combination with the existing equipment and technical features, the stinger adopts the counter-production method. The upper two layers of the main pipe and the diagonal bracing are assembled into pieces. After the welding is completed, the third main pipe is positioned and assembled according to the center line, and finally installed. Both ends of the component.
The A-frame consists of four mainframes, f 711mm×21mm and diagonal braces, 377mm×12mm. It can be divided into upper and lower slabs. Prefabrication is carried out according to the shards during construction. The lower slabs are prefabricated and prefabricated. In the final assembly, the lower piece is first positioned on the tire frame to level, then the vertical support is erected, and finally the upper piece is hoisted for overall assembly, so as to control the overall dimensional accuracy.
The connection structure of the two ends of the stinger and the A-frame is adopted as a "pre-fabricated, integral assembly" construction plan. According to the structural characteristics, the prefabricated construction sequence is: CNC blanking → single prefabrication → nondestructive testing → overall heat treatment → machining.
(5) Welding quality control During the hull welding process, the following points should be noted to improve the overall welding quality. 1 The welding wire and welding rod should be correctly used in suitable conditions and positions, and distributed in an appropriate amount. The time during which the low-hydrogen electrode is exposed to the air must not exceed the specified value. The electrode with the exposure time less than the specified value can be put back into the heat preservation oven, stored at least 120 ° C, and the number of times the electrode must be re-baked is strictly prohibited more than one time. 2 Welds cannot be cooled by quenching or by other methods than air convection cooling. Under some environmental conditions, the weld must be slowed down by covering some insulation material. According to the specific material and environment, take the corresponding preheating and insulation measures. 3 All free surfaces, including decks and their supporting structures, must be sealed with a minimum of 3 mm angular height when they do not have the required weld strength. 4 The joints of the tubular structure can not be welded, and the welding method of single-sided welding and double-sided forming should be adopted. The joints must have appropriate groove to ensure the complete penetration of the weld. 5 When there is a longitudinal joint in the tubular member, the joints of the adjacent two longitudinal slits on the circumferential slit must be staggered by more than 90°. The distance between the longitudinal slits of the two tubular members is ≥ 50 mm. 6 On important structures, including the pile pipe and the main support structure, after the temporary weld is removed, if there is any damage on the surface of the base metal, the part must be 100% magnetic particle inspection. When the 7-pass weld is welded, it is not allowed to be interrupted except for the replacement of the welding rod and the change of the position of the welder. The welding consumables equipment is shown in Figure 9.
4. Conclusion
The Shengli 902 pipe-laying engineering ship not only submitted a quality for the company through the formulation of a reasonable “Chuangyou Engineering†activity plan, as well as strict, meticulous and comprehensive control of each process during the construction process, coupled with the application of new welding technology. Reliable and high-performance engineering vessels have greatly improved the construction capacity and level, laying a foundation for Sinopec Group to develop global offshore petroleum engineering.
Plastics
Plastics Pigment, Plastic Antioxidant, Plastics Organic Pigment, Plastics Solvent Dyes, Calcium Acetylacetonate (CAS No.19372-44-2)
Dynasty Chemicals (NingBo) Co., Ltd. , https://www.dychemco.com