Aluminum substrate features
1. Using surface mount technology (SMT);
2. Very efficient treatment of thermal diffusion in the circuit design method;
3. Reduce product operating temperature, increase product power density and reliability, and extend product life;
4. Reduce product size and reduce hardware and assembly costs;
5. Replace the fragile ceramic substrate for better mechanical durability.
PCB aluminum substrate structure
PCB aluminum-based copper clad laminate is a metal circuit board material consisting of copper foil, thermal conductive insulation layer and metal substrate. Its structure is divided into three layers:
Cireuitl.Layer circuit layer: equivalent to ordinary PCB copper clad, line copper foil thickness loz to 10oz.
Dielcctric Layer: The insulation layer is a low thermal resistance thermal insulation material. The thickness is from 0.003" to 0.006". The core is the core of the aluminum-based copper clad laminate and has obtained UL certification.
Base Layer: It is a metal substrate, usually aluminum or copper. Aluminum-based copper clad laminates and conventional epoxy glass cloth laminates.
The PCB aluminum substrate is composed of a circuit layer, a thermally conductive insulating layer and a metal base layer. The circuit layer (ie, copper foil) is usually etched to form a printed circuit, so that the various components of the assembly are connected to each other. In general, the circuit layer is required to have a large current carrying capacity, so that a thick copper foil should be used, and the thickness is generally 35 μm. 280μm; thermal conductive insulation layer is the core technology of PCB aluminum substrate. It is generally composed of special polymer filled with special ceramics. It has small thermal resistance, excellent viscoelasticity, anti-heat aging ability, and can withstand mechanical and thermal stress. . Thermal insulation layers of high-performance PCB aluminum substrates such as T-101, T-111, T-112, T-113, T-114 and T-200, T-300, T-400, T-500, T-600 This technology is used to make it have excellent thermal conductivity and high-strength electrical insulation properties; the metal base layer is a supporting member of an aluminum substrate, and it is required to have high thermal conductivity, generally aluminum plate or copper plate (where copper plate can Provides better thermal conductivity) for general machining such as drilling, punching and cutting. PCB materials have advantages that are unmatched by other materials. Suitable for power component surface mount SMT public art. No need for a heat sink, greatly reduced size, excellent heat dissipation, good insulation and mechanical properties.
PCB aluminum substrate use
1. Audio equipment: input, output amplifier, balanced amplifier, audio amplifier, preamplifier, power amplifier, etc.
2. Power supply equipment: switching regulator `DC/AC converter `SW regulator, etc.
3. Communication electronic equipment: high frequency amplifier <filtering appliance` reporting circuit.
4. Office automation equipment: motor drives, etc.
5. Car: Electronic regulator `igniter` power controller, etc.
6. Computer: CPU board `floppy disk drive` power supply unit, etc.
7. Power module: Inverter 'solid relay' rectifier bridge and so on.
8. Lighting fixtures: With the promotion of energy-saving lamps, aluminum substrates used in LED lamps have also begun to be applied on a large scale.
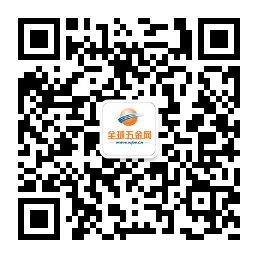
Concerned about surprises
Label: aluminum substrate
Previous: What should I pay attention to when plating silver on aluminum? Next: Performance and application characteristics of zinc and zinc alloys
Heat Shrinkable Tape
I System description:
Heat Shrinkable Tape is designed to protect the weld joint of buried or exposed steel pipelines and insulated pipeline. This sleeves are manufactured from high quality cross linked polyethylene material. Hot melt adhesive provides excellent adhesion with the surface of steel pipeline, PE coating. Meanwhile it forms a continuous and firm anti-corrosive system with the surface of the pipeline.
The Polyethylene Heat shrinkable Tape needs no primer nor patch closure and reduces application time and labour costs.
â…¡ Structure
The specification of the tape consists of three layers,
Adhesive: butyl rubber based hot melt adhesive
Film backing: Radiation crosslinked polyethylene
Interleaf:Antiadhesive Film Treated with Silicone
â…¢ Features
After heating, formed corrosion protection seal
Strong backing provides outstanding waterproofing effect
High chemical resistance. resists impact, abrasion and ultraviolet light.
Excellent resistance against cathodic disbondment, dielectric breakdown.
Simple Application
â…£ Physical Properties
· Product Data Sheet Total Thickness:40mil, 50 mil,60 mil ,65 mils.
· Width:50,100,150,300,400,500,800 mm
· Length: 10 m
· Tensile Strength:35 N/cm
· Elongation:400%
· Adhesion Strength to pipe:30 N/cm
· Application temperature: -10 -60 ℃
· Temperature resistance:-50 ℃ - 80℃
· Shelf Life: 12 months
â…¤ Application
No Special skills, equipments, patch closure nor primer are needed. Its superior flexibility provides easy and reliable application for irregular configurations of fittings, bends and elbows and small diameter of straight pipes
Wrap spirally the tape over foreign matters-free and preheated surface, beginning at least 25~50mm (1~2 ) onto pipe coating. Wrap the tape with enough tension to obtain conformability and with minimum 50% of overlapping, while removing the release liner. Warm the end part of the tape and press down firmly. Using a torch, start at the edge of the tape and heat circumferentially around the coated pipe.
Finish off by heating over the entire tape vertically to ensure a uniform adhesion and by using a roller or gloved hands to remove wrinkle and air.
VI. Technical Datas
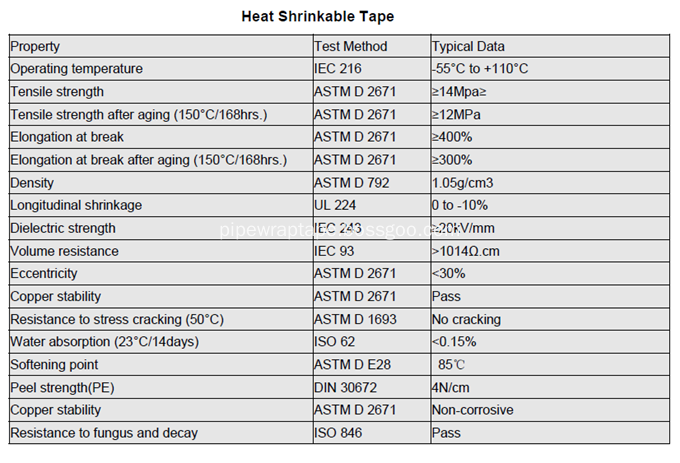

Heat Shrinkable Tape
Heat Shrinkable Tape, Shrink Wrap Tape, Heat Applied Tape
Jining Xunda Pipe Coating Materials Co.,Ltd , http://www.pipe-wrap.com