Modern society cannot do without oil and natural gas. People use pipes to transport these materials from the production plant to the customer. Millions of kilometers of pipelines are found all over the world. If the media flow (such as maintenance work) is to be interrupted, the "valve faucet" must be closed tightly. The high-pressure ball valve can be used to temporarily close the pipeline. This high-pressure ball valve is one of the most important products of RMA Pipeline Equipment.
At the end of the 1960s, the company was founded as a “workshop†factory and a supplier to other companies. As the company grew rapidly, it began developing its own pipe fittings, including ball valves, in the late 1970s. Today, RMA Pipeline is one of the world's leading systems suppliers. Its main business includes the development of various oil and gas, water and district heating pipe fittings, household supply technology, measurement and control technology, and parts tailored to customer specific requirements. RMA employs approximately 500 people worldwide and has two plants in Germany. The Leinau Plant and Administration Center has a total of 200 employees. They have a supporting factory in Kyle, Germany, and one factory in Poland, the United Kingdom, France, the United States, Bahrain and Russia.
Figure 1: The high-gloss surface of the valve plug in the RMA grinding shop. Use Walter corn milling cutter to machine chamfer along the groove Open the tap
The core component of each ball valve is a middle spool, and the middle spool is mounted in a valve body and is rotatable therein. However, these spool sizes used in pipelines are much larger than the spool sizes of our commonly used faucets. The size of the globe valve is in the range of DN 25~DN 1400 mm. Hans-Jürgen Mann ß hardt, head of RMA's manufacturing workshop, said: "Our Lenou plant manufactures products below DN 300 and Kyle manufactures larger sizes." This includes not only spools but also valve bodies. Press, final assembly, coated anti-corrosion polyurethane (PU) plastic coating and final leak test: All high-pressure ball valves from RMA are ready for use at the factory.
Figure 2: High pressure ball valve view of DN 300 flow rate The spool must be well matched
The spool itself is made of rough-worked forged steel and the flow rate through the spool has been approved. In the RMA workshop, there are 30 fully automated lathes and 5 machining centers that undertake all the tasks of producing finished spools from rough parts. In addition to turning and grinding, the cuts required for subsequent processes are made, including the fit above and below the spool. Use a groove that is important for assembly to allow the spool to rotate within the valve body to open or close the valve. The plastic parts and metal races that fit together and are inserted into the valve body with the valve plug ensure a tight seal and no leakage. Plastics can also seal at pressures up to 40 bar, but after more than 40 bar, metal seals are required.
Figure 3: Metal and plastic races meet the high pressure ball valve tightness requirements Therefore, the valve core does not accidentally collide with any part when rotating, and a round chamfer is additionally milled on both sides of the above-mentioned mating surface, which is where the Walter tool expert of Tübingen needs to participate. The total processing time of the 484 mm DN 300 spool on the horizontal machining center is one hour. Up to now, the chamfer requires 10 processes, the processing time is 10 minutes and 30 seconds, and each side is 5 minutes and 15 seconds. To date, this process has been accomplished with other brands of chamfering cutters that have three blades but only one set of teeth.
Figure 4: Using the Walter chamfered corn milling cutter that starts right away (for ease of photography, the machining center table turns a little at an angle to the observer) Increased speed, great popularity
“We have always been very satisfied with the processing performance of the tools used, but one thing is that I want higher efficiency, which is time. I think that a process of more than ten minutes is really too long,†Hans-Jürgen Mann ß hardt said. “So I decided to discuss this with Walter field service staff.†For many years, Michael Benz, an application engineer at Walter in Germany, has been supporting RMA. During the period, he presented and implemented a variety of tooling solutions on site and worked with customers. In an emergency, he can even work all night long. After the discussion, during his next visit, Mercedes-Benz spent a lot of time with the workshop director Mann ß hardt in writing the chamfering process and drafted the initial solution route outline: "The purpose is very clear, that is, Achieve higher metal removal rates. Together we measure directly on the machine to take into account existing toolholders, tool sizes and fixtures, and avoid contour interference.†After a thorough conversation with Hans-Jürgen Mann ß hardt, The Walter consultant then developed the first syllabus: a one-piece tool that does not use any additional interfaces, the structure is as compact as possible and the performance is as stable as possible. Michael Benz said: Old tools are too long and vibration can have a detrimental effect on performance. “The design was sent to Walter's local technical department in Frankfurt for development. Here, the collaborative production department examined the feasibility of tool manufacturing and determined the number and structure of the blade holders.
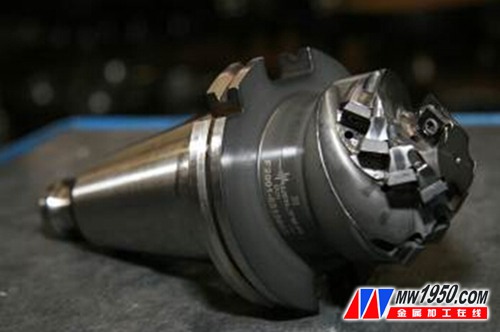
Figure 5: Walter chamfered corn milling cutter, 45° milling angle custom version, three sets of milling cutting edges and four rows of inserts (model F2001-6515665), side view
Special corn milling cutter
As a result, the chamfer milling cutter has a milling angle of 45°, three sets of milling edges and four rows of inserts (model F2001-6515665) as custom tools. "The idea of ​​a corn milling cutter is already in my mind," Mann ß hardt said. “However, due to the angle requirements of the chamfering of the valve plug, such tools are not a standard model and can only be used as a custom solution, as the one that Walter currently implements for us.†What is its performance? The result is obvious. Now, chamfer milling requires only four machining operations for a total time of 6 minutes and 30 seconds (previously 10 minutes and 30 seconds), and the time spent on one side is 3 minutes and 15 seconds (previously 5 minutes and 15 seconds). This is equivalent to a time savings of nearly 40%.
One of the most impressive but not very satisfactory results for Walter employees is: "From our initial discussion, when the RMA began testing in 6 weeks, the blade broke at first, which made us feel a headache. The main problem is Choosing the right cutting tool material," Benz said. "In the end, we decided to use our "unbreakable" toughness material WSP45S, which is our problem solver. It verifies the success of the Walter team as an RMA. Case: Blade breakage never happened again.
Long-term partnership
“We have been working with Walter for about 25 years, and our relationship is a win-win partnership,†Hans-Jürgen Mann ß hardt said. “The valuable experience we have gained during our cooperation is not only in the quality of the tools, but also in large part because of the reliable and solution-oriented service that Walter offers. If the tools are not working well, especially when they are stuck, Walter can always get to the scene to help solve the problem in the first time. It takes only one and a half weeks to completely eliminate the problem with the new chamfer corn milling cutter."
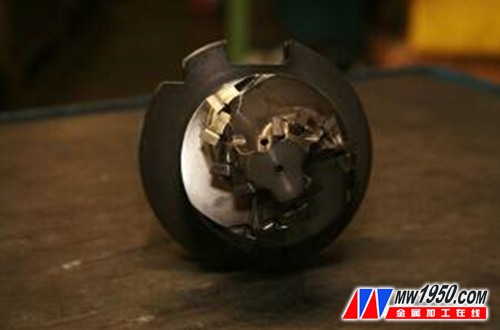
Figure 6: Walter Corn Milling Cutter for Chamfer Milling, Custom Milling Cutter - with 45° Cutting Angle, Three Milling Milling Edges and Four Row Blades (Model F2001-6515665), Front View
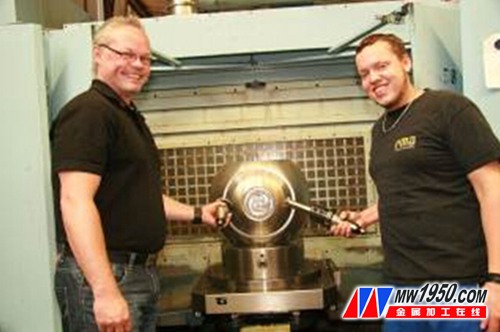
Figure 7: Michael Benz (left), Walter, Germany, and Hans-Jürgen Mann
ß hardt, head of RMA's manufacturing plant,
show new (left) and old (right) milling solutions in front of the spool 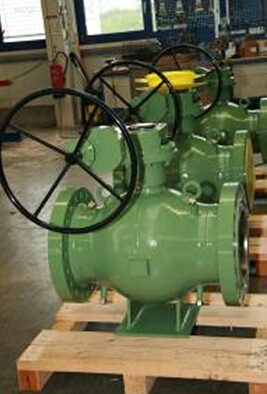
Figure 8: RMA Pipeline Equipment has assembled and painted high pressure ball valves waiting to be shipped
Cow magnets are popular with dairy farmers and veterinarians to help prevent Hardware Disease in cattle. While grazing, cows eat everything from grass and dirt to nails, staples and bits of bailing wire (referred to as tramp iron). Tramp iron tends to lodge in the honeycombed walls of the reticulum, threatening the surrounding vital organs and causing irritation and inflammation, known as Hardware Disease.
The cow loses her appetite and decreases milk output (dairy cows), or her ability to gain weight (feeder stock). Cow magnets help prevent this disease by attracting stray metal from the folds and crevices of the rumen and reticulum. One magnet works for the life of the cow
Cow Magnet
Cow Magnet,Plastic Cow Magnet,Neodymium Cow Magnet Pot,Neodymium Cow Magnet
Chongqing Great Well Magnet Co.,ltd. , https://www.gwmagnet.com