Huaibei Mining Group Electromechanical Equipment Co., Ltd. is a large-scale enterprise mainly engaged in the production of coal mine equipment. In the manufacturing process, there are a large number of parts for the blank production using forging methods, such as the base of the mining unit pillar, the handle body, the piston, The top cover, the four small pieces of the metal top beam, the hydraulic support column, and the cylinder bottom and piston of the jack are all made by die forging. Huaibei Mining Group Electromechanical Equipment Co., Ltd. only produces more than 2000t of blanks for die forging. How to improve the service life of molds is a common concern of our engineers and technicians.
At present, most of the hammer forging materials used in China use 5Cr Ni Mo and 5Cr Mn Mo. Most of our forged blanks are small and medium-sized forgings, and molds made of 5Cr Mn Mo and 5Cr Ni Mo should be used. According to our many years of practical experience, the reasons for the failure of hammer forging die are mostly concentrated in the following aspects: cavity size wear and longitudinal cracks, transverse cracks, and reticular cracks (cracks), so-called thermal fatigue cracks. The causes of these failures are various, involving the problems of raw materials, the microstructure of the forged metal of the mold blank, the reasonable selection of the forging temperature of the mold blank, the geometry of the mold, the heat treatment process and quality of the mold. Taking the hot forging die made of Huaibei Mining Group Electromechanical Equipment Co., Ltd. as 5CrNi Mo and 5Cr Mn Mo as an example, according to the mold use conditions, performance requirements, and the heat treatment process adopted in the mold manufacturing process, etc. Description.
First, the basis of hammer forging die selection
1. Hot forging die working conditions
The hot forging die is subjected to impact pressurization at a high temperature to force metal forming. The mold is subjected to a huge load during the working process, and is subjected to compressive stress, tensile stress and additional bending stress. The forged metal flows in the mold cavity and generates a strong friction force. The surface surface metal is in contact with the high temperature metal and is heated. From 300 to 400 °C, local up to 500 to 600 °C, plus frequent repeated heating and cooling, it is prone to thermal fatigue cracks.
2. Hot forging die performance requirements
Maintain high strength and good impact toughness at working temperature, good thermal ablation resistance (including high thermal fatigue resistance, oxidation resistance and heat strength) and resistance to heat washability and high hardenability, Good thermal conductivity.
According to the working conditions and performance requirements of hot forging die, Huaibei Mining Group Electromechanical Equipment Co., Ltd. selected 5Cr Ni Mo and 5Cr MnMo as the mold materials. The chemical compositions of 5Cr Ni Mo and 5Cr Mn Mo are shown in Table 1.
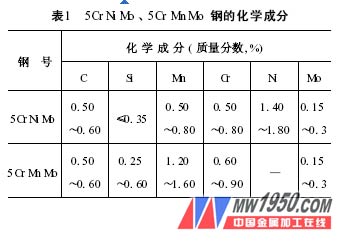
5Cr Ni Mo steel has high hardenability and good comprehensive mechanical properties, and is suitable for manufacturing large forging dies with complex shapes and large impact loads. 5Cr Mn Mo steel replaces Ni with Mn, although the strength is not reduced, but the plasticity and toughness at high temperature are lowered, and the hardenability is lower than that of 5Cr Ni Mo and the superheat sensitivity is slightly larger. Therefore, 5Cr Mn Mo is suitable for manufacturing small and medium forging dies. Hot stamping die.
Second, the mold manufacturing process route
The manufacturing process of hot forging die is generally forging→annealing→forming forming→quenching and tempering. Small molds are processed, quenched, and tempered because of their simple shape, high hardness, and ease of processing. Large and medium forging dies are roughed first, then quenched, tempered and machined.
1. Blank making (forging)
The microstructure and properties of 5Cr Ni Mo and 5Cr Mn Mo hot forging die steels have many similarities with alloy quenched and tempered steels and belong to hypoeutectoid steels. In order to eliminate the directionality of the rolled material structure and make it as uniform as possible to withstand the high stress and impact during work, it must be crushed or forged to destroy its carbide skeleton and reduce the non-uniformity of carbide. . Huaibei Mining Group Electromechanical Equipment Co., Ltd. uses forging method to make blanks. The blanks are upset and lengthened alternately no less than 3 times, the initial forging temperature is 1100 ~ 1180 °C, the final forging temperature is 850 ~ 880 °C, and the total forging ratio is not less than 10, slow cooling after forging to prevent white spots and martensite formation.
2. Annealing
In order to facilitate machining and improve chemical composition segregation and tissue non-uniformity, we usually use a full annealing for pre-heat treatment. Table 2 shows the complete annealing process parameters of Huaibei Mining Group Electromechanical Equipment Co., Ltd.
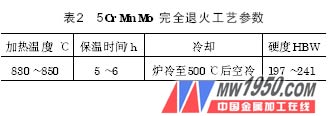
Next page