It can be concluded that the coarse ferrite + pearlite structure obtained by isothermal normalizing by forging waste heat can be re-refined in the subsequent carburizing heating to obtain fine and uniform austenite grains. Studies have shown that heating the original microstructure to ordered coarse grained structure (non-equilibrium martensite, bainite, etc.) may result in the formation of austenite grains of the same shape, size and orientation as the original microstructure. Tissue genetic phenomena appear. When the original structure is heated to the equiaxed pro-eutectoid ferrite and pearlite equilibrium structure, the properties of the coarse grains are fundamentally changed, and the grains can be re-refined.
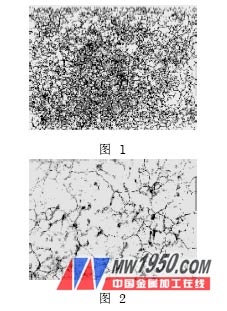
3. Effect of isothermal normalizing on deformation of parts after carburizing and quenching
The conventional bevel gears of the rear axle reducer made of 22CrMo steel are subjected to ordinary normalizing and isothermal normalizing treatment. After machining and carburizing and quenching, the deformation of the parts is compared. In the comparative deformation test, the machining process of each part and the heat treatment carburizing and quenching process are guaranteed to be the same, thereby comparing the effects of ordinary normalizing and isothermal normalizing on the deformation of the part. The deformation requirements of the follower reducer driven bevel gear are: flatness ≤0.10mm, ellipticity ≤0.08mm. Each of the 100 randomly selected parts is measured, and the deformation distribution of the parts pretreated to ordinary normalizing is shown in Fig. 3. The deformation distribution of the parts pretreated to isothermal normalizing is shown in Fig. 4.
After the bridge reducer driven bevel gear is used as an example for deformation analysis, 100 pieces of unqualified parts with ellipticality and flatness are randomly sampled in the finished parts pre-processed as ordinary normalized, a total of 29 pieces, the deformation meets the requirements. The qualified rate was 71%. It can be seen from Fig. 3 that the deformation data is concentrated in the upper limit ratio, which is 60.7%, and the deformation data is only 10% to 15%, and the sample is very poor. Too large, the sample mean is biased to the upper limit of technical requirements. It can be seen that the pre-treatment is a normal normalized part. The distribution of deformation statistics after carburizing and quenching is not a reasonable distribution, and the degree of data dispersion is large. In the finished parts pre-processed to isothermal normalization, 100 pieces were randomly sampled, and 2 parts with unqualified ellipticity and flatness were used. The qualified rate of the deformation conforming to the requirements was 98%. As can be seen from Fig. 4, the inner hole and plane deformation data are concentrated, and 85% to 90% of the deformation data falls in the middle and lower limits, and the sample range and the mean value are also relatively small. It can be seen that the pre-treatment is an isothermal normalized part. The distribution of deformation statistics after carburizing and quenching is reasonable, and the probability density curve is approximately normal distribution.
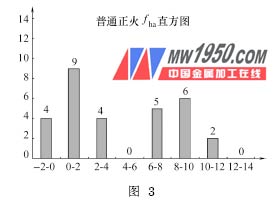
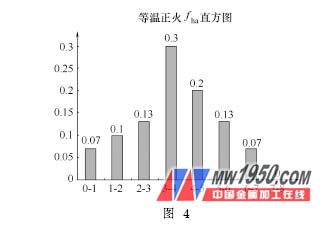
Fourth, the conclusion
(1) Ordinary normalizing of alloy carburized steel forging blanks, since the phase transition is continuously carried out in a temperature range, the austenite transformation cannot be controlled. Isothermal normalizing can effectively control the phase change during cooling, so that the phase transition can be carried out at isothermal temperature, and the uniform microstructure and hardness can be obtained.
(2) Using the isothermal normalizing of the forged residual heat, the coarse austenite grains form an equilibrium structure (ferrite plus pearlite), and the fine uniform austenite grains can be regained in the subsequent carburization heating.
(3) Because of the isothermal normalizing, the microstructure and hardness required for uniform uniformity can be obtained. The pretreatment uses isothermally treated parts to reliably achieve good machinability and stable quenching deformation.
(4) The use of forging waste heat isothermal normalizing can greatly reduce costs and improve product quality, with significant economic and social effects.
Previous page