Thorough testing of the safety and reliability of electric vehicle batteries is essential, but, so far, laboratory tests have been very unrealistic. To this end, according to foreign media reports, researchers from the Fraunhofer Association in Germany have developed a new test environment that combines physical components with the mathematical simulation of vehicles to become the first device to conduct laboratory tests under real conditions. .
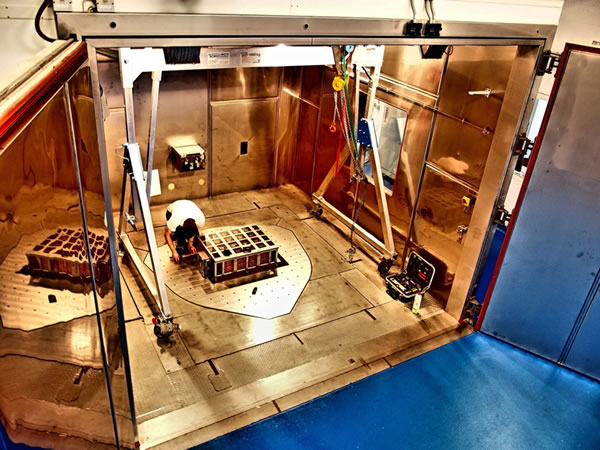
(Source: Fraunhofer Institute for Structural Stability and System Reliability)
Electric vehicle batteries are often called power batteries, and are the key components of electric vehicles. Storing the energy provided by the charging station and supplying power on demand is one of the functions of the battery performance equation. The other is to deal with sharp turns, bouncing on gravel-filled roads, and driving cars in the scorching heat. The battery needs to resist wear caused by electricity, machinery, and thermal stress. Therefore, the new battery system must undergo various tests before it can be installed on the vehicle. However, traditional laboratory tests are far from reality, and real-world tests must wait until engineers produce prototypes that can be driven. If the problem is not discovered before the battery appears in the later stage, it may take a lot of time and money to improve the battery.
Researchers at the Fraunhofer Institute for Structural Durability and System Reliability LBF (German Fraunhofer Institute for Structural Durability and System Reliability LBF) have developed an alternative solution, MEF-BILL, which is Battery in the Loop. abbreviation of. LBF researchers said: "We are now introducing real road conditions into the laboratory, and combining multi-physics test equipment and computerized vehicle simulation technology means that we can test the battery under real conditions before the prototype car exists. In this way, we can invest a lot of time in the research and development process, and can significantly improve the quality of battery research results."
The load on the battery mainly comes from three aspects-the load mainly caused by current, vehicle movement and climate factors. Traditional methods will test the above three factors separately in a laboratory with a standard operating environment. However, in the real world, the three factors are interdependent and affect each other in complex ways. Researchers can simultaneously test such loads and their interactions in the test environment, and integrate computerized vehicle models in real time in the test environment. In this way, researchers can simulate the vehicle and its performance on different types of roads, thus being able to determine the load that exists in the real world and affects the battery under actual conditions.
In the past, the test of battery current distribution in the laboratory was usually performed according to an ideal curve, but in real life the curve will look very different, the change trajectory is highly dynamic, changes randomly, and will suddenly change unpredictably with the appearance of load peak Therefore, the researchers first need to determine the test conditions. What type of car does the battery power? How heavy is the load? How fast is it? Is the road surface flat, smooth or pothole? When calculating the applied load and the current of the test battery, the simulation will take all factors into account in this performance equation. The experts conducting the battery test also took into account this complex interaction. For example, the initial power requirement will vary with battery temperature or other parameters. The researchers continuously track the actual parameters of the battery and continuously feed back the parameters to the simulation system. This tracking feedback loop constitutes a hardware-in-the-loop test. Throughout the testing process, the input is not always static data. Instead, it is dynamically adjusted based on battery simulation and battery data. The researchers said: "We can reproduce the real driving action in the test scenario, such as uphill or downhill or sharp turns." You can also study how other variables affect performance, for example, to determine when the increased load will make the vehicle quality What happens when it increases by 20%. Vibration testing can also be performed, using a vibration table driven by six hydraulic cylinders, and can be moved in any direction to simulate the impact of the car chassis on battery movement.
One of the biggest challenges of hardware-in-the-loop testing is that the simulation must be performed in real time. For example, if you conduct a test to investigate a 10-second operation, the entire simulation may take no more than 10 seconds. After all, this is a loop test, and the results of the simulation must be directly fed back to the test in order to dynamically update the simulation as the test progresses. Researchers have fine-tuned the complexity of the calculation to make it work. The researchers said: "We run simulations at different levels of complexity to achieve the best balance between complexity and computing time." The system is ready for use, and final preparations for the demonstration are still in progress. (Yu Qiuyun)
Pu Resin For Inks
Custom Logo Print Inks,Pu Resin For Inks,Solvent Based Printing Inks,Waterproof Water-Based Ink
XUCHUAN CHEMICAL(SUZHOU) CO., LTD , https://www.xuchuanchem.com