Our company specializes in the production of slurry pumps for more than 20 years. The core over-current components (impeller, volute, front and rear guards, etc.) of the pump products are made of high-corrosion-resistant and corrosion-resistant high-chromium alloy to meet the power plant. In addition to ash, desulfurization, dredging of rivers and clearing sands, as well as mining and mineral processing, such as the wear and corrosion conditions of the transporting granular slurry.
In the production practice, the general thickness of the high-chromium alloy castings, in the casting using ordinary sand-type riser can meet the requirements of the casting shrinkage. However, with the increase of the wall thickness or structural limitation of the high chromium alloy parts, especially when making the overflow parts of large dredging pumps, the ordinary sand type feeders have poor feeding effect, shrinkage, cracking, sanding and leakage. The problem is serious, resulting in a low yield and a large loss. Therefore, problems such as shrinkage and cracking of large castings have become an urgent problem to be solved.
The new type of heat-insulating riser and heat-generating covering agent has a significant effect on the feeding of the castings, but how to operate in the casting process of high-chromium alloy materials, how to organically combine with other elements in the casting process, we need to explore and practice.
1. High chromium alloy casting characteristics
High-chromium alloy cast iron is a white cast iron. Due to its wide crystallization temperature range, it is easy to form coarse grains during solidification. It has poor casting properties, large shrinkage, low thermal conductivity and high brittleness. It is prone to heat during casting. Cracking and cold cracking tendencies, as well as defects such as shrinkage and shrinkage.
2. Heat insulation riser and heat cover agent characteristics
The heat-insulating riser is a riser sleeve made of a heat-insulating material or a heat-generating material. When the pouring, the heat released by the heating material in the riser heats the metal liquid which is lower in the temperature rising into the riser, and then the heat insulating material in the riser starts to burn and heat, which reduces the heat loss of the molten metal and delays the solidification time of the molten metal in the riser. .
The hot covering agent covers the surface of the riser after the pouring of the molten iron, and can effectively isolate the molten metal from dissipating heat through the upper surface of the riser, thereby achieving long-term feeding of the casting.
3. Implementation of technical content
In order to strengthen the feeding effect of large-scale high-chromium castings, we have a detailed understanding of the new technology and selection calculation method of the heat-insulating riser with the heating cover agent, combined with the characteristics of the high-chromium alloy material, after repeated trials and tests, The process plan and implementation steps were formulated to achieve better results.
(1) Selection of riser to calculate the modulus of casting and the amount of molten metal required for solidification of the casting. Calculate the modulus of the required riser according to the riser modulus method. Through practice, take the riser modulus as the casting modulus. 1.3 to 1.5 times. The feeding distance is determined by considering the casting material, structure, temperature gradient, and pressure conditions and metallization treatment. Combine the component structure to determine the style specification, quantity and placement of the riser.
The material of the high-chromium casting material shrinks greatly, and the amount of shrinkage required for the solidification of the casting is large. In the design of the riser, the full and effective feeding of the casting by the riser should be considered, that is, the riser design should be as large as possible. However, since it is a brittle material, the riser is increased, which may cause the stress of the casting to increase, and crack defects are easily generated. Therefore, the rationality of the riser design is very important.
(2) Realizing the sequential solidification of castings If it is necessary to avoid casting defects such as shrinkage and shrinkage, the metal liquid at the riser should be solidified later than the casting, and the riser should have enough molten metal to fill the casting. The feeder is fed to the casting passage to achieve sequential solidification. For large tonnage castings, a double gating system is used to ensure that the pouring of molten iron is carried out during the casting time and process temperature.
(3) After the second point riser poured the molten iron at the site, it was found that the amount of molten iron was not enough to be filled, and the riser appeared hollow. Therefore, measures are taken to carry out the secondary point pouring after half an hour of pouring, that is, to refill the iron liquid for all the risers, and to maintain the amount of iron liquid to ensure the effect of feeding.
(4) After the molten iron is poured, the heat-generating covering agent is applied to the surface of the rising riser to effectively isolate the molten metal from the upper surface of the riser by heat radiation and heat convection, thereby reducing heat transfer and increasing the riser. safe distance. At the same time, long-term heat preservation can strengthen the shrinkage, and is also conducive to the gas precipitation in the casting and the floating of the inclusions, and obtain a sound casting, reducing the scrap rate.
(5) Configuring high-temperature resistant coatings, heat-insulating risers, high heat generation, long heat-acting time, usually zircon powder coatings used on sand-type surfaces can not withstand high-temperature combustion, thus burning cast sand molds, and it is easy to cause serious sand sticking on the surface of castings. It is very difficult to clean up on site. Therefore, a specially configured high temperature resistant coating containing a large amount of zirconium and good penetration resistance is used to solve this problem.
(6) Easily cut pieces are placed on the bottom of the riser, and the riser can be hammered and knocked off to reduce the cleaning time and cost of cutting and polishing.
4. Application effect
(1) In the large marine pump parts, the volute contour size is 5200mm × 1200mm, the wall thickness is 110mm, the casting weight is 15t, and the resin sand is molded. In order to reduce the size of the riser, the process design uses 10 sets of FR300 heat insulation riser and heating cover agent, set double pouring system, and with other auxiliary measures, the process feeding effect is remarkable, avoiding shrinkage, shrinkage and sand phenomenon.
The large volute riser is set as shown in the drawing.
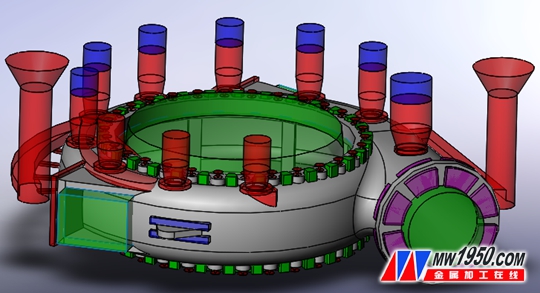
Large volute riser setting diagram
(2) In the casting process of large-scale desulfurization pump volute, the material is made of anti-wear and corrosion-resistant high-chromium alloy material developed by our company. Its body shrinkage is large, it tends to paste-like solidification, casting process is very poor, easy to produce Microscopic shrinkage defects cause many leak points if a sand-type riser is used. The technical problem of the volute pressure leakage can not be solved. To this end, we optimized the casting process. The casting system introduces molten iron into the cavity through the riser, and places 10 Φ150mm small heat risers inside the volute sand core to fill the lower box castings. 10 small heat risers were designed in the upper box, and a large FR300 heat riser was placed in the exit section to fill the castings in the upper box, and the covering agent was added later in the pouring, with other technical measures to effectively stop Microscopic shrinkage defects are generated inside the casting, which is ideal for preventing the pressure leakage of the volute.
Through many tests and verifications, the use rules of the heat-insulating riser and the heat-generating covering agent are summarized, and the shaping process is formed, which provides an effective casting process for the production of large-wall thickness and large-heat-high chromium alloy castings.
Cutlery Set
Stainless Steel Flatware,Kitchen Stainless Steel Flatware,Flatware Set Cutlery Set
YANGJIANG TRI-WIN INDUSTRY & TRADE CO.,LTD , https://www.triwintableware.com