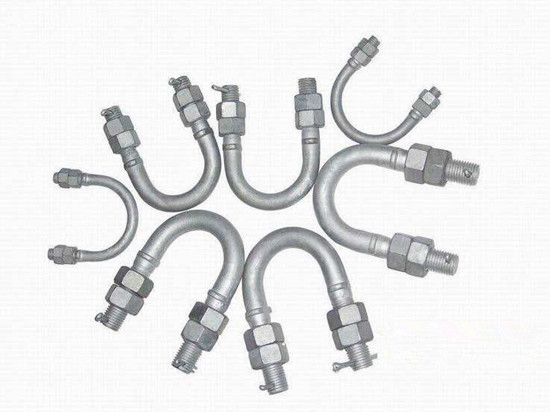
First, the significance and role of galvanizing
Hot-dip galvanized u-bolts are one of the most commonly used fasteners because of their importance and long-term maintenance during their use. One of the most important ways to maintain is to prevent oxidation of the u-bolt. This is what we usually call rust-proof treatment. One of the most effective methods is galvanizing. Zinc plating refers to a surface treatment technique in which a layer of zinc is plated on the surface of a metal, alloy or other material for aesthetics, rust prevention, and the like. The main method used is hot dip galvanizing.
The national standard for hot-dip galvanizing is GB/T 13912-2002 "Technical requirements and test methods for hot-dip galvanizing of metal-clad steel parts". The metal after galvanizing should be smooth in appearance, free of zinc, burrs and silver. White; thickness is controllable, arbitrarily selected within 5-107um; no hydrogen embrittlement on the surface, no temperature hazard, can ensure the mechanical properties of the material is unchanged; can replace some processes requiring hot-dip galvanizing; metal resistance after galvanizing Corrosive, neutral salt spray test for 240 hours.
Galvanizing has a wide range of applications, such as steel nails, nails, fasteners, various hardware fittings, scaffolding fasteners, and so on.
Second, several common galvanizing methods
According to the difference in surface color after galvanizing, there are eight common methods of galvanizing, electroplating white zinc, blue and white zinc, multicolored zinc, blackening, chrome plating, hot-dip galvanizing, plating, and natural color.
Third, the common factors affecting galvanized screws
(1) Pre-treatment is not thorough. The surface of the workpiece has an oxide film that affects the normal deposition of zinc.
(2) Poor electrical conductivity. The current is consumed on the wire and the current distributed to the surface of the workpiece is too small.
(3) The workpiece has a high carbon content. High carbon steel, cast iron parts, etc. will reduce the precipitation potential of hydrogen, accelerate hydrogen evolution on the surface of the workpiece, and reduce current efficiency.
(4) The workpiece is tied too densely. When the galvanizing is partially shielded, the coating is too thin.
(5) The bath temperature is low. When the bath temperature is low, the current density of the distribution is correspondingly reduced, and the deposition speed of the plating layer is also inevitably lowered.
(6) The sodium hydroxide content in the plating solution is high. When the sodium hydroxide content is high, the current efficiency is correspondingly reduced.
(7) The additive content in the plating solution is low. Low levels of additives can affect the dispersing ability, and the coating is partially too thin.
(8) The estimated area of ​​the plated part is insufficient, and the current density delivered during plating is too small.
(9) The workpiece suspension method is improper, and the distance between the zinc anode and the anode is too large, and the position should be adjusted.
(10) The workpiece is over-etched. The hydrogen evolution potential is lowered, and hydrogen evolution on the surface of the workpiece accelerates the current efficiency, thereby affecting the deposition rate of zinc. An appropriate amount of corrosion inhibitor should be added to the pickling solution. The local scale is too thick to be removed by mechanical means, and more inspection is carried out during the pickling process.
(11) Anode passivation. The effective area is reduced, which affects the normal distribution of current.
(12) The sodium hydroxide content is low. If the sodium hydroxide content is low, the current density is not high and the anode is passivated.
Fourth, the types and advantages and disadvantages of galvanizing
According to the galvanizing method and the different requirements of customers, the most commonly used galvanizing processes for u-bolts are electrogalvanizing, powder zincizing, mechanical galvanizing, hot dip galvanizing, etc. Advantages and disadvantages;
1. Electro-galvanizing, electro-galvanizing is the most common surface treatment method and process technology in the manufacture of fastener products. The electro-galvanized layer is a typical anodized coating and is mainly used to improve the corrosion resistance of the substrate. Due to its thin coating thickness, it is mainly used for surface corrosion protection under general environmental conditions.
After chromate passivation treatment, its anti-corrosion performance is greatly improved. The excellent electro-galvanized layer can be used for outdoor protection against neutrality, but the corrosion resistance is poor in harsh industrial atmosphere and coastal climate.
The electroplating zinc surface treatment method and process technology have low cost, stable and reliable process and convenient use. However, it is highly prone to hydrogen embrittlement, so dehydrogenation should be carried out in time after electroplating. In addition, the acid and alkali resistance is poor, the corrosion time is short, and the process environmental protection is low.
2, powder zinc infiltration, powder zinc infiltration is a zinc source for the zinc source, and by heating to produce zinc, iron atoms interdiffusion and surface treatment process in the steel surface zinc dip layer (zinc-iron alloy layer).
The main component of powder zinc infiltration is pure zinc powder, in which an appropriate amount of filler materials such as alumina, refractory earth and ammonium chloride are added.
The most prominent feature of powder galvanizing is not an external coating, but the base metal and the permeable layer form an organic unit, so the combination is very strong. The hardness and corrosion resistance of the powder zincized layer is much better than that of the electrogalvanized layer.
In the powder zinc infiltration process, the surface-treated workpiece is buried in a sealed container filled with a powder galvanizing agent, heated to a melting point of zinc, kept for a certain period of time, and then cooled to room temperature with the furnace.
The most prominent feature of powder zinc infiltration is that the layer is uniform, there is no ammonia brittle, and there is almost no deformation. It is especially suitable for fasteners such as nuts, bolts and other small hardware products, complex shapes and surface anti-corrosion treatment of powder metallurgy products.
3, mechanical galvanizing, mechanical galvanizing in the presence of zinc powder and dispersant, accelerator, liquid medium (usually water) and other conditions, the use of impact media (such as glass balls), impact impact on the surface of steel parts, A surface treatment process is formed on the surface of the workpiece to form a galvanized layer.
The mechanical galvanizing layer is an anti-corrosion coating formed by a process different from electrogalvanizing and hot-dip galvanizing. Process characteristics: The production operation at room temperature conditions, through the rotation of the plating cylinder of the loading part, the impact medium in the cylinder rotates with the drum, and the parts collide with each other to generate mechanical impact force, and the zinc powder collides and deposits on the surface of the workpiece, thereby forming A coating having the basic physical characteristics of metallic zinc.
Process characteristics: The galvanizing process of the mechanical galvanizing process does not cause hydrogen embrittlement damage to high-strength steel.
Process defects: the thickness of the zinc layer is uneven; the zinc layer is not as smooth and bright as the plating layer.
4, hot dip galvanizing, hot dip galvanizing is also commonly known as hot-dip galvanizing hot-dip galvanizing is the pre-treatment of steel parts into the molten zinc liquid, forming zinc and / or zinc-iron alloy on its surface The process and method of coating to obtain a metal coating.
Hot dip galvanizing applications are extremely extensive, such as hot dip galvanized highway traffic barriers (highway corrugated beam guardrail fasteners), hot dip galvanized fasteners for pipes and power transmission, and others Fasteners, etc.
The service life of the hot dip galvanizing work is directly related to the process itself, and has a direct relationship with the adhesion amount of the galvanized layer.
The hot-dip galvanized layer has good protection against the atmospheric corrosion and is superior to electro-galvanized.